The need for a Steel Research and Innovation Programme
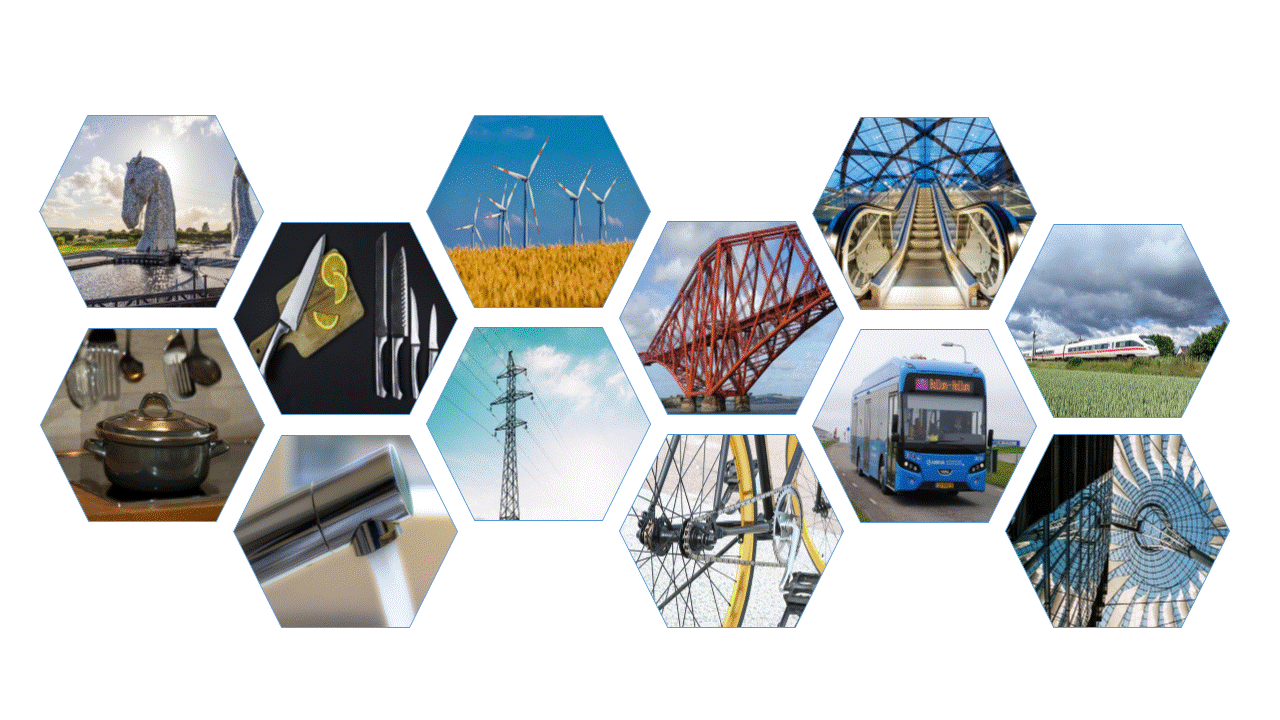
The steel industry is a sector with historically high CO2 emissions. However, in Sweden, companies are taking the lead towards more sustainable production using fossil-free hydrogen and bio carbon fuel sources and reduction agents. This research program will go further to assess the properties of steel produced by hydrogen and recycled materials - as well as explore radically new production processes.
About steel
Steel is an important material that defines our modern world. The novel combination of durability with both hardness and flexibility means that steel is used in many applications. Applications include pipelines to distribute clean water and for wastewater recycling equipment, construction, vehicles, appliances and much more.
Steel is produced by combining pure iron atoms and carbon and, optionally, alloying elements such as chrome, nickel, vanadium and magnesium. There are 1000s of different types of steels, called grades. The steel grade is determined by the use of specific combinations of alloying elements as well as the heat treatments - the outcome of which when examined through a microscope is a steel bulk that comprises small, densely packed, crystal grains that are randomly orientated. It is the chemical composition of the crystals, together with their grain size and grain size distribution, that distinguish the grade of steel.
The Swedish steel industry
Offering specialist steel grades is the basis for the Swedish steel industry to compete globally against low cost countries. Moreover, as consumers and regulators increasingly set requirements on minimising the release of greenhouse gases, the Swedish steel industry is also competing based on its relatively small climatic footprint.
The relatively small climatic footprint of the Swedish steel industry can be traced back to before the 1970s. At that time, regulations led to more effective processes that avoided the release of particles into the air as well as the production of waste materials. Competition from lower cost countries led to a focus on process efficiency as well as specialisation - the production of specialist steels.
Today, Sweden has the lowest greenhouse gas emissions in the world. Sweden also has the highest use of recycling. Nonetheless, steel making still requires significant use of energy to melt iron and for the high temperature heat treating processes. Moreover, coking coal has been key to steelmaking for over a thousand years. This means that the steel industry has a high carbon dioxide footprint. Nonetheless, times are changing.
The Swedish steel industry in transition
Steel companies in Sweden, especially in the Norrbotten region, are taking a world-leading position in the industry's transition to more sustainable production. Starting with mining, LKAB are making annual investments of billions of SEK towards decarbonisating iron extraction and iron-ore processing. The steel company SSAB wants to be the first to launch fossil-free steel on the market in 2026 - by reducing the iron ore into pure iron using hydrogen instead of coal and coke. Furthermore, new companies have established themselves and set the aim to produce green steel from 2025. This includes Stegra (formerly know as H2GreenSteel), which is establishing a new hydrogen energy plant and steel plant in the Norrbotten region. Elsewhere in Sweden, steel companies such as Outokumpu and Ovako and steel powder producer such as Höganäs, are decarbonising their production processes that use recycled material inputs.
These breakthrough climate innovations however pose the question of what else can we do to support sustainable transitions in the steel industry.
Questions for the future Swedish steel industry
Some questions that the Steel for a Fossil Free Future Programme poses, and aims to answer, include:
- What happens to the quality of engineered steel products, and slag (a bi-product of steel), when using hydrogen?
- How can we overcome today's limits to producing quality engineering steel products when using recycled materials?
And,
- Can we design radically new processes for producing steel from iron-ore?
To support answering these, and other questions, our research focuses on understanding the fundamental reactions that occur during the hydrogen reduction process, recycling processes, and steel treatment processes - and, how these reactions affect the properties of steels. We will also investigate alternative materials and processes.
Our research towards fossil-free steel
"Steel for a fossil-free future" has objectives to shape advanced theory, models and practical knowledge related to the design and production of new advanced, materials engineered, steel products - where production avoids the use of fossil fuels, avoids wastes and uses sustainably sourced and recycled materials inputs. The intent is to support the iron and steel industry in the Norrbotten region, and Sweden generally, to accelerate the industry’s transition to climate-neutral production with reduced carbon dioxide emissions.
The research is organised into the following work packages.
- Influence of hydrogen on properties of fossil-free steels
- Alloy design for fossil-free steels
- Control of the hydrogen content in fossil-free steels
- Optimized scrap utilization
- Influence of temperature gradients and microstructure on hot-rolled sheet and strip
Funded by the EU's Just Transition Fund and Tillväxtverket
Steel for a Fossil-free future is funded by the EU’s Just Transition Fund and Tillväxtverkt (the Swedish Agency for Economic and Regional Growth) with co-financing from KTH and LTU. The Just Transition Fund addresses regions at risk from structural changes in industries operating their regions, as such industries make changes to reduce climate impacts.
This particular programme funding aims to supporting the Norrbotten region in the transition to a hydrogen based economy. Therefore, the "Steel for a Fossil Free Future" programme has industrial stakeholders such as SSAB and LKAB (due to their activities in the region) and Jernkontoret (the Swedish iron and steel producers' association) due to the need to disseminate the new knowledge more broadly.
The programme value is 41 MSEK over 4 years.